B.Tech. Engineering Technology
The technology of this age is truly interdisciplinary. Technologists with a multi-domain perspective have an advantage over the specialists and such graduates are sought-after by the engineering enterprises.
The seven-semester B.Tech. Engineering Technology programme under the Work Integrated Learning Programme for working professionals is designed to provide this advantage to the learners. The programme provides a broad intellectual foundation in contemporary technologies while developing the relevant engineering fundamentals and introduces the important methods of technology practice.
Option to pay fees using easy EMI option with 0% interest
Programme Highlights
- Industry-relevant curriculum, delivered online or on-site lectures.
- The programme positions the professionals out of narrow technology domains thus enabling them to gain an overall perspective to address the engineering field, which has evolved to be interdisciplinary.
- A blend of foundational sciences, core technologies and execution management develops a rounded professional competence, which is a requirement for strong professional development.
- Students learn to use contemporary computation tools such as PTC Creo, MATLAB, Flownex and Remote lab on Fluid Mechanics, which build the technical skill and competency of the students thus enhancing their professional value.
- The Dissertation (Project Work) in the final semester enables students to apply concepts and techniques learnt during the programme.
- The programme uses a Continuous Evaluation System that assesses the learners over convenient and regular intervals. Such a system provides timely and frequent feedback and helps busy working professionals stay on course with the programme.
- The education delivery methodology is a blend of classroom and experiential learning. Experiential learning consists of lab exercises, assignments, case studies and work-integrated activities.
- Participants who successfully complete the programme will become members of an elite & global community of BITS Pilani Alumni.
Programme Curriculum
Participants need to take at least 12 courses towards coursework, and complete one Project/ Dissertation. The coursework requirement for the programme would consist of a set of core courses and electives. Core courses are compulsory for all participants, while electives can be chosen based on individual learning preferences.
The programme offers a degree of customisation to address the specific L&D needs of your organisations.
- Electrical & Electronics Technology
- Calculus
- Engineering Materials
- Computer Programming
- Probability & Statistics
- Linear Algebra & Optimization
- Engineering Measurements
- Mechanical Technology
- Manufacturing Processes
- Engineering Design
- Production Planning & Control
- Maintenance & Safety
- Instrumentation & Control
- Materials Management
- Essentials of Project Management
- Plant Layout & Design
- Quality Control, Assurance & Reliability
- Elective 1
- Elective 2
- Elective 3
- Principles of Management
- Technical Report Writing
- Elective 4
- Elective 5
- Project Work
- Energy Management
- Environmental Pollution Control
- Flexible Manufacturing Systems
- Manufacturing Excellence
- Mechatronics & Automation
- Microprocessors & Microcontrollers
- Management Information Systems
- Additive Manufacturing
- IoT in Manufacturing
- Connected Cars
- Advanced Driver Assistance Systems
Learning Methodology

LECTURES DELIVERED ONLINE AND ONSITE
Lectures are delivered by BITS Pilani faculty members through live via online classes, or at the organisation's premises, and are designed to offer similar levels of interactivity as regular classrooms at the BITS Pilani campus.
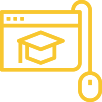
DIGITAL LEARNING
Learners can access engaging learning material at their own pace which includes recorded lectures from BITS Pilani faculty members, course handouts and recorded lab content where applicable.

CONTINUOUS ASSESSMENT
Continuous Assessment includes graded Assignments/ Quizzes, Mid-semester exam, and Comprehensive Exam.

EXPERIENTIAL LEARNING
The programme emphasises on Experiential Learning that allows learners to apply concepts learnt in the classroom in simulated, and real work situations. This is achieved through:
- Simulation Tools, Platforms & Environments: Some or all of the following would be utilised across the programme.
- Simulation environments for Circuits such as LabView & MultiSim
- Modelling & Analysis using PTC Creo & MATLAB
- Thermal Engineering concepts using Flownex Simulation tool and Fluid Mechanics Remote Labs
- Manufacturing process simulation using Afdex & Zcastpro
- Manufacturing management using FlexSim

CASE STUDIES AND ASSIGNMENTS
Carefully chosen real-world cases & assignments are both discussed and used as problem-solving exercises during the programme.

DISSERTATION/ PROJECT WORK
The fourth semester offers an opportunity for learners to apply their knowledge gained during the programme to a real-world like complex project. The learner is expected to demonstrate understanding of vital principles learnt across semesters and their ability to successfully apply these concepts.
Online Labs & Remote Labs

VIRTUAL LAB
The Virtual Lab is a cloud based simulation space, where participants can design, develop and test solutions for industry scale problems. The lab hosts a range of popular software tools that can simulate the complete spectrum of engineering processes to the accuracy and precision of real-life. The lab is open 24x7, 365 days with a live support.
Industrial Engineering Virtual Lab
Manufacturing management is a 3D simulation platform that models, simulates, predicts, and visualizes systems in manufacturing, material handling, healthcare, warehousing, mining, logistics, etc. Participants can use the Industrial Engineering Virtual Lab to perform experiments such as Lean Manufacturing, Flexible Manufacturing Systems, and Operations Management.
Engineering Design Virtual Lab
Engineering Design Virtual Lab helps in understanding the implementation of various design process approach involves in all level of design, assembly, drafting and analysis of components to the real-world problems. Through the Engineering Design Virtual Lab, participants can perform experiments such as; Developing different mechanical parts and assemblies with various design needs, Create assemblies with kinematic and constrain basis.
Metal Forming Virtual Lab
Advanced metal forming technology yields high productivity of mechanical parts, allowing mass production. However, development of metal-forming processes takes a great deal of time and cost. Virtual lab contribute for improving process design and engineering of all forming processes with short span of time. Participants can use the Metal Forming Virtual Lab to perform experiments such as Simulation of cold and hot forging process, Die structural analysis.
Heat Treatment Virtual Lab
In this lab users can enter the heating, cooling and tempering heat treatment cycle for virtually treating complex geometry for a defined period of time. Users are allowed to graphically evaluate microstructure property changes and predict the abnormalities likely to occur during the cycle. Participants can use the Heat Treatment Virtual Lab to perform experiments such as Annealing process of a forging die, tempering process of a test specimen.
Machining Virtual Lab
Development of metal cutting processes, tool design, cutting parameters and controller settings takes a great deal of time and cost. Virtual lab contribute for improving process design and engineering of all CNC metal removal processes with short span of time. Participants can use the Machining Virtual Lab to perform the experiments such as 3 & 5 Axis machining with Siemens, Fanuc, Haas, and Mitsubishi controllers, turning with Fanuc & Siemens controller.
Circuits Virtual Lab
Creating complex layer of Printed Circuit Boards (PCB) with varying level of circuits requires great understanding of technologies related to electrical and electronics. Circuits’ virtual lab provides the users to simulate complex circuits and prototype the PCBs. Participants can use the Circuits Virtual Lab to perform experiments such as Simulate and plot the characteristics curves of RC, RLC, single phase transformers, and capacitors, Simulate the circuits and logics in Multisim and implement with Labview interface.
Virtual Lab using Matlab
MATLAB (matrix laboratory) is a multi-paradigm numerical computing environment and proprietary programming language. Matlab is used for computer programming, mathematical modelling such as geometry, dynamics & robotics, and MIL simulations. Participants can use the Virtual Lab using Matlab to perform experiments such as Computer programming experiments, Model in the loop & hardware in the loop testing using Simulink.
LabVIEW Virtual Lab
Virtual lab using Labview provides the users to create a virtual hardware interface for any engineering application that requires test, measurement and control and provide PC based data acquisition boards and simulate the digital circuits. Participants can use the LabVIEW Virtual Lab to perform Engineering Measurements related experiments, and Instrumentation and control related experiments.
Thermal Engineering Virtual Lab
Thermal simulation enables to study how systems will behave in the real world, where fluid is the driving factor. Virtual lab which relays the overall effect of changing specific properties on components, allowing users to examine extensively all possible variations in the design and optimization of systems. Participants can use the Thermal Engineering Virtual Lab to perform the experiments with pumps, turbines, valves, composite pipes, fluids, gasses and other flow related components, thermodynamic components.
Automation Studio Virtual Lab
Automation Studio offers intuitive design, animation, simulation and system analysis functionalities in a versatile and user-friendly environment in Mechatronics and Automation domain. It allows students to build and select their mechatronics circuits including hydraulic, pneumatics, electronic, electrical, PLC and combination of these elements. Participants can use the Automation Studio Virtual Lab to perform experiments such as PLC programming for specific automation processes, Hydraulics and pneumatics circuit simulation using different control valves.

REMOTE LAB
Through the Remote lab, participants can perform controlled experiments from anywhere in the world. The IoT enabled lab equipments and the integrated remote access network makes this possible. The lab is open 24x7, 365 days. Remote Lab is one more attempt by the work integrated learning programs division of BITS Pilani to bring the campus learning experience to the working professionals complementing their work-life-learning balance.
Synchronous Motor Setup
This equipment includes the synchronous motor and single phase alternator setup. Participants are allowed to interact with the motor by varying the frequency and record the responses. Participants can perform experiments such as calibrating the motor with the frequency inputs, Alternate residual voltage test.
Asynchronous Motor Setup
This equipment includes the asynchronous motor and DC generator setup. Students are allowed to interact with the motor by varying the frequency and record the responses of the motor. Participants can perform experiments such as Load test with variable frequency drive, No load and open circuit test.
DC Motor Generator Setup
This equipment includes the DC motor and three phase alternator setup. Students are allowed to interact with the motor by varying the armature voltage and record the responses of the motor. Participants can perform experiments such as Speed control of DC motor, Residual voltage and speed vs. power test
Experiments with Liquid Level Control
This experimental unit is designed for the purpose of various modern control methods laboratory testing and applications. The liquid level in the tank is measured by a pressure sensor using the height of the water column and is transmitted as an electric voltage signal. Liquid level control model represents a typical loop control system. Participants can perform experiments such as P control on liquid level loop, PI control on liquid level loop
Experiments with Position Control
This experimental unit is designed for the purpose of various modern control methods laboratory testing and applications. The liquid level in the tank is measured by a pressure sensor using the height of the water column and is transmitted as an electric voltage signal. Liquid level control model represents a typical loop control system. Participants can perform experiments such as P control Positioning loop, PI control Positioning loop, PID control Positioning loop.
Experiments with Pressure Control
In this setup pressure tank is charged with compressed air by a diaphragm gas pump. The pressure is measured using a pressure sensor. The sensor output signal is sent to the software controller. The output signal from the controller influences the speed of the diaphragm gas pump and hence the flow rate. Participants can perform experiments such as Continuous P control of reference variable pressure, Continuous PI control of reference variable pressure, Two point pressure control.
Experiments with Fuzzy Control
Fuzzy methods are particularly suitable for systems that mathematics cannot describe adequately or easily. A fuzzy control is used to attempt to hold the ball in a specific position by tilting the beam, even when the position of the ball is modified by external influences. The position of the ball is determined using a resistive measuring system. A potentiometer detects the inclination of the beam. Participants can perform experiments such as Continuous P control of reference variable pressure, Continuous PI control of reference variable pressure, Two point pressure control.
Experiments with Temperature Control
In this experiment temperature is measured using a thermal resistor (PTC). A metal bar, which is thermally insulated with cladding, is heated or cooled at one end by a Peltier element. Participants can perform experiments such as Continuous P control of reference variable temperature, Continuous PI control of reference variable temperature, Two point temperature control.
Experiments with Flow Control
A flow control is used to control the flow of liquid in the tank. The rota meter offers the advantage that the flow rate can be observed directly at any time. The flow rate is measured by a turbine wheel flow sensor. Participants can perform experiments such as Continuous P control of reference variable speed, Continuous PI control of reference variable speed, Two point speed control.
Experiments with Speed Control
In this experiment a DC motor drives a shaft with a mass flywheel. The dial gauge allows the speed to be read off directly at any time. The speed is measured inductively using a speed sensor. Participants can perform experiments such as PI control, PID control of a disturbance variable.
Experiments with Axial Fan using AR
Axial fans are used to transport gases. The medium to be transported is drawn in axially to the drive shaft of the axial fan by the rotation of the rotor. The medium flows through the rotor and is discharged axially behind the rotor. This experiment is accessed through augmented reality enabled mobile platform. Students shall get interact in 3D space using AR technology. Participants can perform experiments such as Dependencies and fan characteristics, Dependencies, system characteristics, operating point.
Experiments with Radial Compressor using AR
Radial compressors are used to compress gases. The medium is drawn in axially to the drive shaft by the rotation of the rotor and flows through the rotor rotating at high speed. By means of centrifugal force, the medium is accelerated towards the outer edge and is compressed in this manner. This experiment is accessed through augmented reality enabled mobile platform. Students shall get interact in 3D space using AR technology. Participants can perform experiments such as Dependencies and compressor characteristics, Dependencies, system characteristics, operating point
Heat Conduction and Convection
Heat conduction and convection experiment setup allows basic experiments on both forms of heat transfer: heat conduction and convection. Heat Transfer range are equipped with electronic sensors for PC-based measurement data acquisition and are operated from a PC for different samples (Copper, Steel, Aluminium and Brass). Participants can perform experiments such as Dependencies and compressor characteristics, Dependencies, system characteristics, operating point
Experiments with Pelton Turbine
Pelton turbines are types of impulse turbine. They are driven by free jet nozzles. The water jet is accelerated in a nozzle and hits the Pelton wheel tangentially. The impulse of the water jet is transmitted to the Pelton wheel. Participants can perform experiments such as Relationship between turbine speed and pressure, Variation of the volume flow with the needle valve.
Experiments with Piston Pump
Piston pumps belong to the group of positive displacement pumps. They transport the medium by a reciprocating motion of a piston in the pump working space, called stroke. The stroke creates a suction hence vacuum effect used to deliver the water. Participants can perform experiments such as p,V diagram, time graphs and phase difference. Dependencies and pump characteristics, Pulsating dampening.
Experiments with Actuators board
This board is designed exclusively for the NI ELVIS III platform and LabVIEW, the Quanser Mechatronic Actuators board exposes students to industry-grade measurement and command fundamentals for the four most common actuator types: brushed DC motors, brushless DC motors, stepper motors, and servo motors. Participants can perform experiments such as Brushed and Brushless DC Motors, Linear and PWM Amplifiers, Power Amplifier Design Considerations.
Eligibility Criteria
Minimum eligibility to apply: Working professionals holding Diploma in Engineering/ B.Sc. in relevant disciplines, with at least 60% aggregate marks and minimum of two years of work experience after the completion of the degree in relevant domains.
The programme is designed for:
- Highly driven and ambitious engineers who wish to gain deep insight into Core Engineering, Manufacturing and Executive Management functions
- Experienced professionals aspiring to gain an overall competency in the popular technology domains, which sets them apart from narrow specialisations